Join us at our 6th Printed Electronics Days Conference where industry experts will share their knowledge on cutting-edge and specialized topics from various angles and first-hand. With a lineup of engaging lectures, you'll explore the entire process chain, from functional inks and printing techniques to market insights and best practice applications.
Registration fee € 370,00 excl. VAT per person
Venue: Empire Riverside Hotel Hamburg, Bernhard-Nocht-Str. 97 , 20359 Hamburg, Germany
Looking at the customers of ContiTech, there three segments: Automotive Interior, Living solutions and Industrial products. They all have a different pace in terms of innovation cycles or new products, depending on the individual product life cycles and requirements. And from a product manufacturer perspective it is not even important if the functionality is printed or made of traditional electronics. It needs to fit the requirements and the cost. In essence: By looking through the eyes of the customer, we must understand, where printed functionalities will fit and develop accordingly.
PyzoFlex® is a fully printed sensor technology based on a printable polymer ink. The transducer is manufactured using a screen printing process, which enables printing of customized sensors of specific shape and size on a variety of substrates including plastic film, paper, glass and metal. Our ferroelectric sensor ink allows a system to detect changes in temperature (∆T; pyroelectric), pressure (∆P; piezoelectric) as well as structure born sound (Hz; vibration). Due to the sensing principle of PyzoFlex®, the transducers themselves do not require a power supply and in fact can also be used for energy harvesting. The talk gives an overview of the Pyzoflex technology and many application examples.
Innovative Sensor Technology iST AG, a leading manufacturer of a diverse portfolio of predominantly physical sensors, has established a strong reputation for its core competence in thin film platinum resistance temperature detectors (RTDs). Over time, the company has expanded its expertise to encompass various other sensor principles. Along with other microfabrication techniques, such as sputtering and micro welding, screen printing is one of iST’s central processes for sensor fabrication. Attendees will gain valuable insights into how printing technologies are integrated into the production of temperature sensors, conductivity sensors and heaters, among others. Potential for printing as an enabling technology is discussed. Moreover, the presentation will address the obstacles encountered in the printing process and shed light on how iST AG overcomes these challenges.
The presentation highlights recent advancements in fine-line screen printing and printed electronics at Witte Technology GmbH, enabling smart solutions in healthcare, building security, and industrial applications. A key focus is the development of printed leakage sensors for medical devices and sustainable buildings. Together with customers, Witte has established an accelerated life testing (ALT) methodology to predict long-term product reliability at the prototype stage, achieving an acceleration factor of approximately 73 - allowing a three-month test to simulate up to 19 years of real-world aging without inducing artificial failure mechanisms. The work demonstrates the potential of functional screen printing for harsh applications in various industrial applications. The Partnership with ELANTAS supports the transition from prototyping to mass production, rethinking the boundaries of industrial-scale printed electronics.
The presentation highlights recent advancements in fine-line screen printing and printed electronics at Witte Technology GmbH, enabling smart solutions in healthcare, building security, and industrial applications. A key focus is the development of printed leakage sensors for medical devices and sustainable buildings. Together with customers, Witte has established an accelerated life testing (ALT) methodology to predict long-term product reliability at the prototype stage, achieving an acceleration factor of approximately 73 - allowing a three-month test to simulate up to 19 years of real-world aging without inducing artificial failure mechanisms. The work demonstrates the potential of functional screen printing for harsh applications in various industrial applications. The Partnership with ELANTAS supports the transition from prototyping to mass production, rethinking the boundaries of industrial-scale printed electronics.
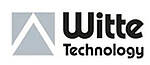
Dr. Phillip Renners
Vice President of Research & Development
Witte Technology GmbH
Sara Shishegaran
Product Developer
Witte Technology GmbH
As printed electronics continue to push the boundaries of flexible, lightweight, and cost-effective electronic systems, the role of surface engineering becomes increasingly critical. Atmospheric pressure plasma (APP) technology—operated in open air without vacuum systems—offers a versatile and scalable solution to meet these evolving demands. This presentation explores how APP can enhance key process steps in printed electronics manufacturing. Plasma-based surface treatment significantly improves ink adhesion by increasing surface energy on low-energy substrates such as PET and polyolefins, enabling reliable and high-resolution printing. In addition, plasma cleaning and activation support the removal of organic contaminants and the functionalization of surfaces, crucial for achieving robust interlayer bonding in multilayer and hybrid devices. Finally, APP shows promise in enabling or modifying encapsulation and barrier layers, protecting moisture-sensitive components like OLEDs and biosensors. While these applications are already part of the printed electronics landscape, the full potential of atmospheric plasma remains far from fully realized. This presentation invites a broader discussion on where and how APP can further optimize existing processes, overcome current limitations, and open new paths in the design and performance of printed electronic systems.
The demand for smart, connected solutions is rising rapidly – and with it, the market potential for RFID applications in industrial manufacturing. In particular, the field of printed electronics is opening new avenues for cost-efficient, large-scale, and flexible production of intelligent components. However, these opportunities also bring growing demands for process reliability and product quality. Ensuring functionality is a key challenge, especially in the demanding and dynamic printing process broken or incompletely printed conductive tracks, as well as geometric deviations, can significantly impair the performance of RFID tags – while being barely visible to the naked eye. High-resolution, optical 100% inspection systems offer a solution here: operating in a roll-to-roll (R2R) rewinder, they detect defects on already printed RFIDs in real time, document them digitally, and classify them with pinpoint accuracy. This enables the targeted identification of defective units – a vital step towards reliable and reproducible quality assurance. There is potential in the intelligent networking of relevant quality data: when optical inspection results are combined with other inline measurements – for instance, to verify the RFID encoding capability – a comprehensive defect profile emerges. This not only provides the basis for immediate process intervention but also enables data-driven optimization across the entire production chain. Solutions already implemented by technology providers such as BST demonstrate how digital quality assurance can become a strategic success factor in RFID production.
Diode lasers are by far the most efficient method of generating thermal energy in NIR-absorbing materials. Fortunately, most conductive inks, e.g., Ag and Cu from ELANTAS, absorb the 940 nm wavelength of Hamamatsu SPOLD lasers. This allows a homogeneous sintering result in combination with standard substrates. Using laser line optics enables scalable yet highly sustainable high-volume production in an R2R system. Hamamatsu's collaboration with ELANTAS on several pre-studies demonstrates the entire process chain from material to process developments and offers benefits for printed electronics manufacturing, such as saving machine space and energy costs.
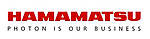
Alexander Goerk
Business Development Manager Industrial Optoelectronic Components
Hamamatsu Photonics Deutschland GmbH
As the demand for scalable, cost-effective, and sustainable materials in printed electronics continues to grow, copper is emerging as a promising alternative to silver in conductive ink formulations. This panel discussion brings together experts from industry and research to explore the technical, economic, and environmental implications of this material transition. Join us for an in-depth exchange on the opportunities and limitations of copper-based solutions in the evolving landscape of printed electronics.
Motivation
The vision: Full-surface active ambient lighting on vehicle surfaces using a high density of RGB light points — setting new standards in design, functionality, and user experience.
The goal is to create an emotional, daylight-visible customer experience through intelligent lighting integration, while maximizing efficiency and cost-effectiveness.
Advantages
- High light intensity with low energy consumption
- Minimal package size – ideal for tight installation spaces
- Efficient in both production and operation
- Cost savings through scalability and modular design
- Flexible design changes – fast and easy customization
- Recyclability – sustainable and future-ready
Implementation Requirements
- Fulfillment of all relevant test conditions, including performance across a wide temperature range
- Minimal scrap rate – process reliability and consistent quality
- Vertical integration or access to an existing, capable supplier network
Vision
The use of cost-effective components with high functionality that can be staged in a way that is visibly engaging and daylight-capable, making light a tangible, emotional, and brand-defining design element.
We use electric heaters in our everyday life, where many applications are just simple wire heaters like your toaster or hair dryer. In cases where a wire heater can't be used, printed electronics create some benefits with flat and flexible printed heaters. Going through several steps of improvement and optimization, the transition from a simple wire heater towards a sophisticated and complex printed heating solution will be shown.
In many situations it is important to know about the health of other people. Whether it is your staff, elderly people or soldiers. If a person falls or is injured, it is urgent to help. Retrieving this information as fast as possible, while not compromising comfort and usability is enabled by Printed Electronics. Stretchable inks, artificial intelligence and smart processes make all this possible.
Printed electronic circuits (PEC) represent an innovative approach to electronics manufacturing, offering the potential to create flexible, lightweight, and cost-effective devices. This presentation will discuss the key aspects of PEC technology, with a particular focus on printing techniques such as flexography. Flexography, as one of the most versatile printing methods, enables the deposition of conductive and semiconductive materials on various substrates, including polymer films and paper. The advantages and challenges associated with using flexography in the production of electronic circuits will be presented, along with examples of applications such as sensors and antennas. The aim of the presentation is to showcase the potential of flexography in the context of modern electronic technology development and to inspire further research and innovation in this field.
This joint presentation explores the potential of processing functional pastes not only through traditional screen printing but also via advanced digital printing technology. ELANTAS develops screen-printable silver formulations optimized for conductivity, adhesion and formability, while Quantica’s high-viscosity jetting technology enables the digital deposition of materials with viscosities and particle sizes far beyond conventional inkjet capabilities. The talk will address the rheological and particle dispersion requirements for jetting silver-based pastes and discuss challenges such as nozzle clogging, optimizing ejection parameters for complex rheology and stable material cycling. Initial joint results will be presented, followed by a technical outlook.